In today’s competitive business environment, companies are constantly seeking ways to reduce costs while maintaining high product quality. Cost reduction strategies in production play a crucial role in ensuring businesses remain profitable without sacrificing the integrity of their products. Achieving this balance requires careful planning, process optimization, and innovation. Companies that successfully manage to reduce production costs while upholding quality standards often gain a significant competitive edge in the marketplace.
This article will explore effective cost reduction strategies that can be implemented in the production process. These strategies are designed to optimize resources, streamline workflows, and minimize waste, all while maintaining the high standards that customers expect. Let’s dive into the practical approaches that businesses can adopt to reduce production costs without compromising on quality.
1. Process Optimization for Cost Efficiency
The first step in reducing production costs without sacrificing quality is optimizing existing processes. Process optimization involves examining every aspect of the production line to identify inefficiencies and areas for improvement. By streamlining workflows, companies can minimize unnecessary steps and reduce operational costs.
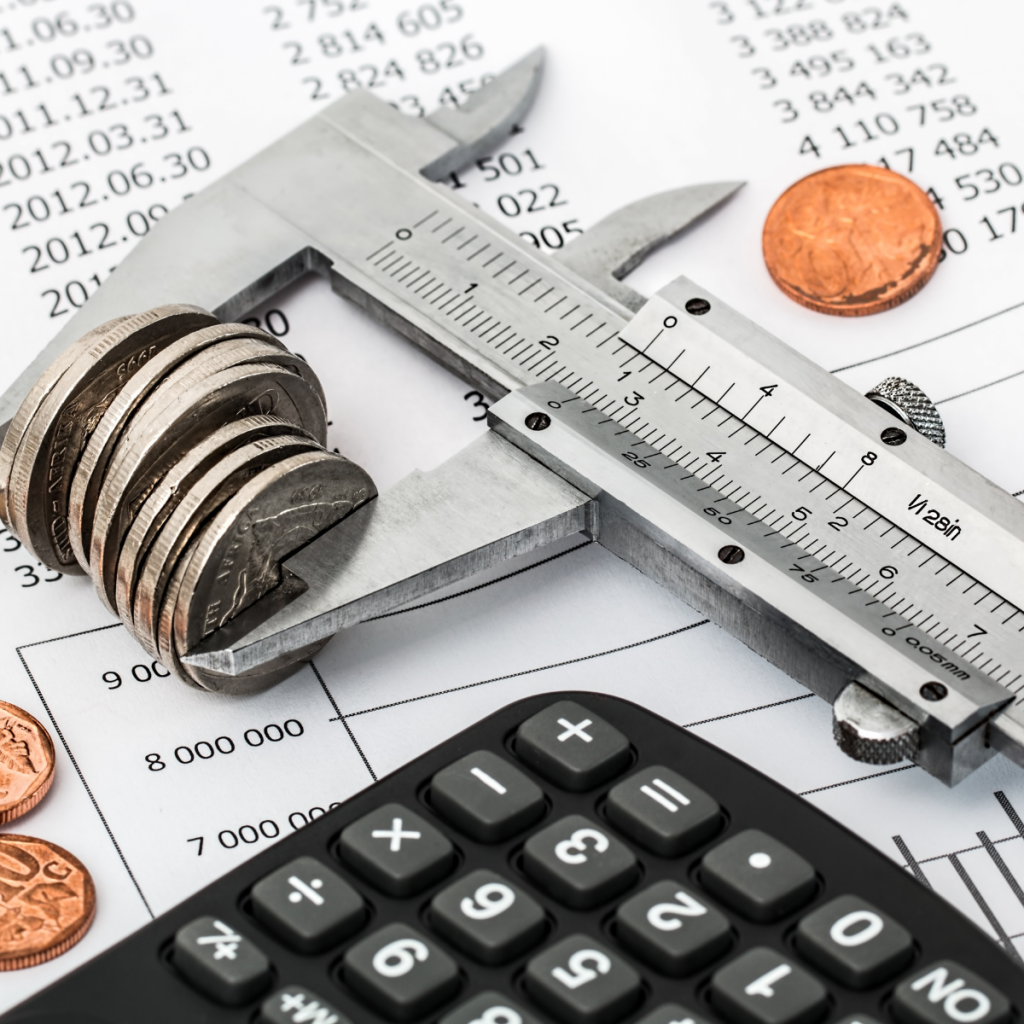
Lean Manufacturing Techniques
Implementing lean manufacturing principles is one of the most effective ways to optimize production processes. Lean manufacturing focuses on eliminating waste in all forms, including time, materials, and labor. By adopting lean practices such as continuous improvement (Kaizen), companies can refine their processes, reduce downtime, and minimize the cost of production.
For example, companies can reduce excess inventory, improve equipment maintenance schedules, and shorten cycle times. These changes not only lower production costs but also ensure that quality standards are maintained by focusing on efficiency and reducing errors.
Automation and Technology Integration
Incorporating automation and advanced technology into the production process can lead to significant cost savings. Automated systems can handle repetitive tasks with precision, reducing the need for manual labor and decreasing the likelihood of errors. Automated machines can work around the clock, increasing production output and reducing labor costs while ensuring high-quality output.
Additionally, technology integration such as real-time monitoring and control systems allows businesses to track production performance and identify bottlenecks. This ensures that any issues are detected and addressed promptly, preventing delays and maintaining production standards.
2. Improving Supply Chain Efficiency
A streamlined supply chain is essential to reducing production costs. By enhancing supply chain management, businesses can cut down on transportation costs, optimize inventory management, and minimize delays. Effective supply chain management ensures that the right materials are available when needed, without overstocking, which ties up capital.
Vendor Relationship Management
Building strong relationships with suppliers and negotiating better terms can lead to reduced material costs. Companies can work with suppliers to implement just-in-time (JIT) inventory systems, ensuring that materials are delivered as needed, reducing storage costs and the risk of waste.
Additionally, establishing long-term relationships with reliable suppliers can lead to discounts, better credit terms, and more favorable delivery schedules. These benefits can directly impact production costs while maintaining a steady supply of high-quality materials.
Bulk Purchasing and Material Substitution
Another strategy to reduce production costs without compromising quality is bulk purchasing. By buying materials in bulk, companies can secure lower prices and reduce per-unit costs. Bulk purchasing is particularly useful for materials that are used frequently in production.
Furthermore, companies can explore material substitution—finding alternative materials that provide the same or better quality at a lower cost. This may involve working closely with the research and development (R&D) team to identify cost-effective substitutes that do not compromise the final product’s quality.
3. Energy Efficiency and Sustainability Initiatives
Energy costs are a significant factor in production expenses. By adopting energy-efficient practices and sustainability initiatives, companies can reduce their energy consumption and lower production costs. These efforts not only help save money but also align with growing consumer demand for environmentally friendly businesses.
Implementing Energy-Efficient Equipment
One of the most effective ways to reduce energy consumption is by upgrading to energy-efficient machinery and equipment. Modern equipment is designed to consume less energy while delivering the same or better performance. By investing in energy-efficient technology, companies can cut utility bills and lower overall production costs.
For instance, switching to LED lighting, optimizing heating and cooling systems, and using energy-efficient motors can significantly reduce energy usage in manufacturing facilities. This approach helps to control costs while supporting sustainable business practices.
Sustainability in Materials and Processes
Incorporating sustainability into the production process can also reduce costs in the long run. Companies can look for ways to reduce waste, recycle materials, and use renewable resources. Implementing green production practices not only reduces material costs but can also improve brand image and customer loyalty.
For example, using recycled materials can lower the cost of raw materials while appealing to environmentally conscious consumers. Additionally, reducing waste through efficient production techniques minimizes the need for costly disposal and handling.
4. Employee Training and Engagement
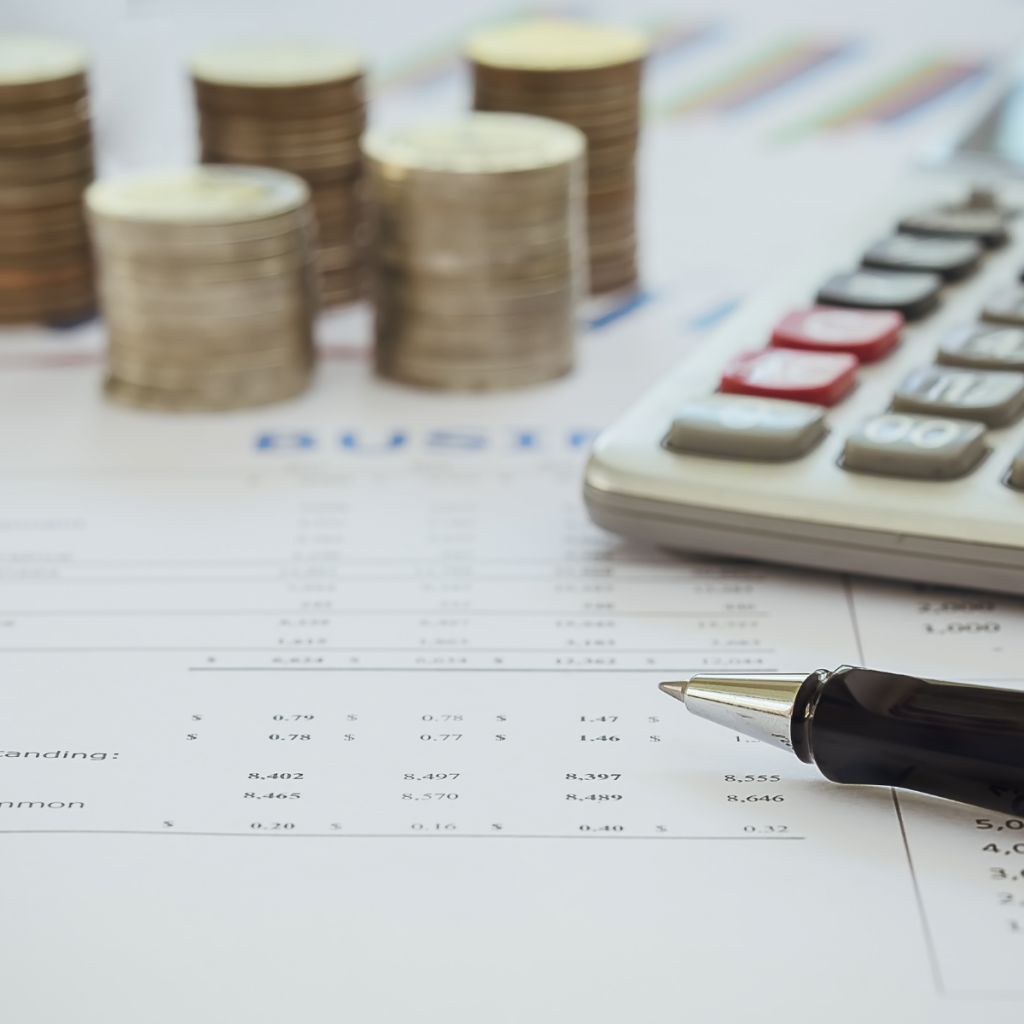
Employees are one of the most valuable assets in any business, and their skills and knowledge play a critical role in maintaining both cost-efficiency and quality. Investing in employee training and engagement can lead to improvements in productivity, safety, and overall performance, ultimately reducing production costs.
Training for Skill Development
Training employees on the latest production techniques, safety protocols, and equipment can enhance operational efficiency and reduce costly mistakes. Skilled employees are less likely to make errors that lead to product defects, rework, or delays, thus saving the company money.
Regular training on lean manufacturing practices, process optimization, and quality control can help employees understand the importance of minimizing waste and maintaining high production standards. This knowledge empowers workers to contribute to cost-saving initiatives and improve the production process.
Fostering a Culture of Continuous Improvement
Encouraging employees to participate in a culture of continuous improvement can lead to long-term cost savings. When employees are actively involved in identifying inefficiencies, suggesting process improvements, and solving problems, they can help implement cost-reduction strategies effectively.
Involving employees in decision-making processes and rewarding innovation fosters a sense of ownership and responsibility, leading to increased motivation and better overall performance.
5. Quality Control and Standardization
While cost reduction is essential, maintaining product quality is non-negotiable. Therefore, implementing strict quality control measures and standardizing production processes ensures that cost-cutting strategies do not negatively impact the final product. By ensuring consistent quality across every stage of production, businesses can avoid costly product defects, returns, or reputational damage.
Standard Operating Procedures (SOPs)
Standardizing production processes through clear Standard Operating Procedures (SOPs) ensures that every step in the production line follows best practices. SOPs guide workers to perform tasks consistently, minimizing errors and improving efficiency. By following a set procedure, businesses can maintain quality while reducing variability, which ultimately lowers costs.
Regular Quality Audits and Inspections
Implementing regular quality audits and inspections at different stages of the production process helps detect defects early, preventing costly rework and product recalls. By investing in quality assurance and continuous monitoring, businesses can ensure that cost-saving efforts do not result in a decline in product quality.
6. Outsourcing and Contract Manufacturing
Outsourcing certain parts of the production process can be an effective strategy for cost reduction. By partnering with third-party manufacturers or contract manufacturers, companies can take advantage of economies of scale and reduce overhead costs associated with maintaining in-house production facilities.
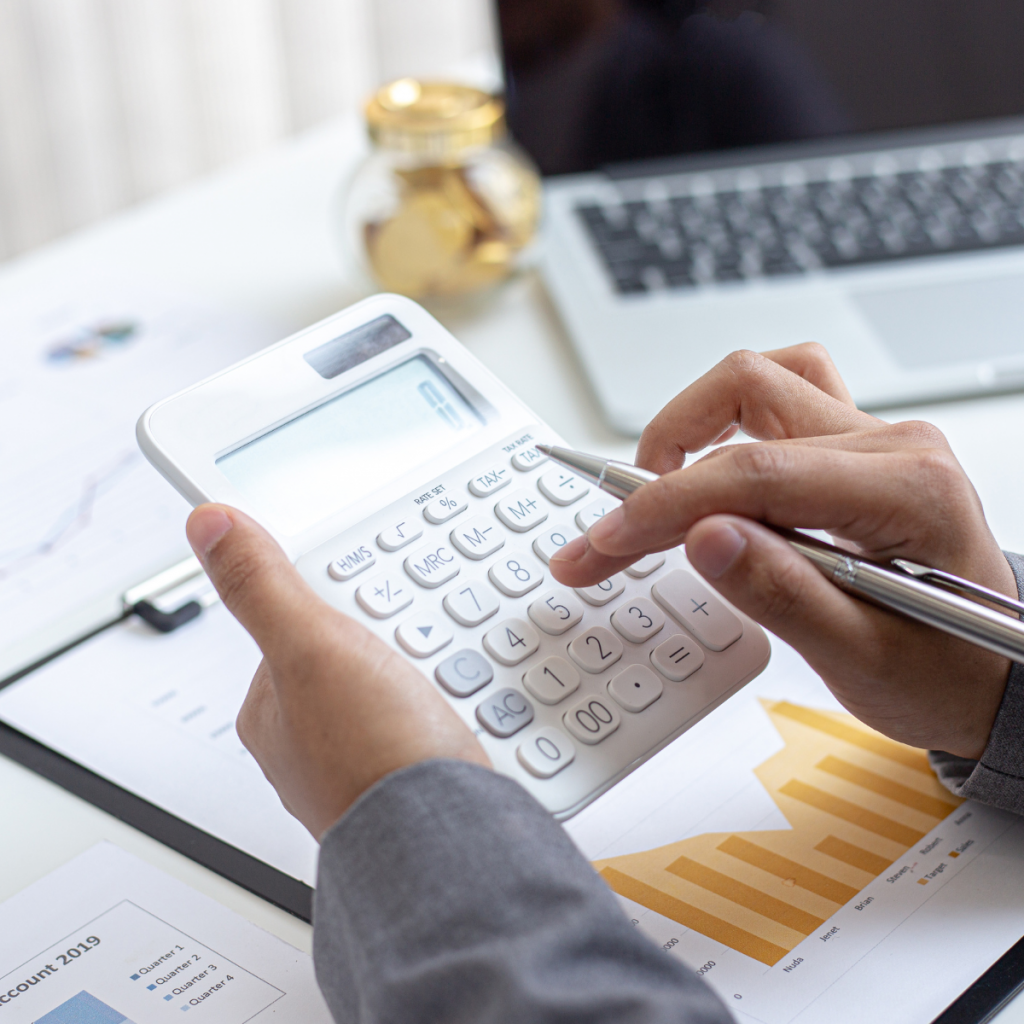
Outsourcing allows businesses to focus on core competencies and leave non-core tasks, such as assembly or packaging, to specialists. Contract manufacturers often have access to advanced technologies and established supply chains, which can further reduce costs while ensuring high-quality products.
Conclusion
Reducing production costs without compromising quality is a delicate balance that requires a comprehensive approach. By optimizing processes, enhancing supply chain efficiency, investing in energy-efficient technology, and empowering employees, businesses can achieve significant cost savings. At the same time, maintaining strict quality control and adopting innovative strategies ensures that the final product remains competitive in the market.
Adopting these strategies enables companies to improve their profitability, sustain long-term growth, and build a strong brand reputation based on both cost efficiency and high-quality products. With the right approach, businesses can navigate the challenges of cost reduction while staying true to their commitment to quality.
Leave a Reply